Why a focus on behavioural safety may prove more effective than physical controls
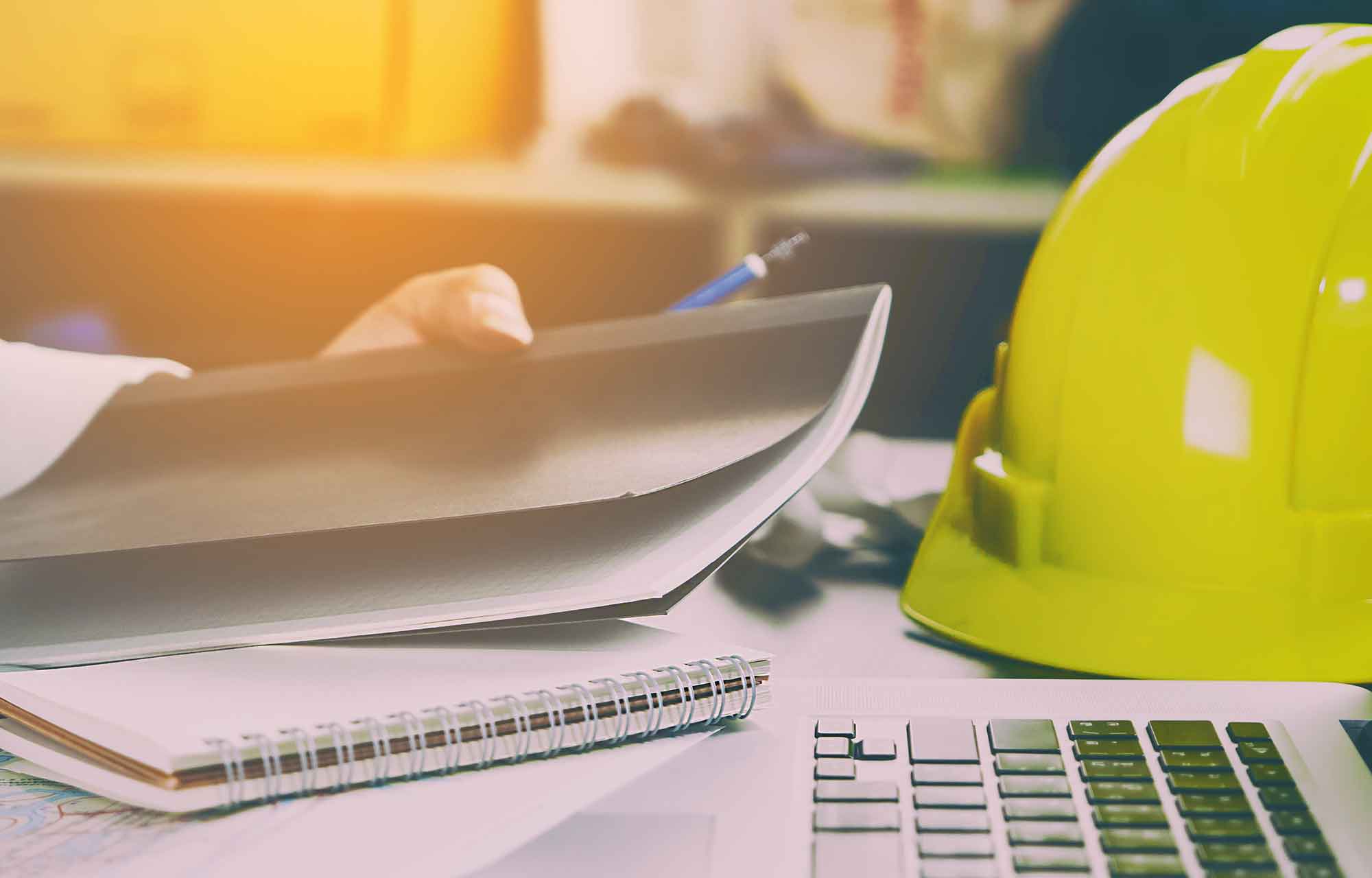
In the workplace, unsafe behaviour is responsible for a huge percentage of accidents, approximately 90%.
Every year, the Health and Safety Executive (HSE) produces work-related injury and ill-health statistics. While the long-term rates of injury and ill health show a general downward trend, incident numbers have been broadly flat in recent years.
The question is, why?
In the war on workplace accidents, physical preventative weapons such as machinery guarding may only go so far. As such, when it comes to slicing through the accident ‘plateau’, turning your attention to behavioural safety may be the key to combating workplace accidents and driving the numbers down.
What is behavioural safety?
Behavioural safety is the name given to a range of initiatives that aim to improve safety by changing workers’ behaviour. This ‘human factor’ approach is also referred to behavioural modification.
Behavioural safety has been around since the 1930s. While most common in production industries, it is an approach that is relevant to all sectors. Proponents of behavioural safety believe that workplace accidents are invariably triggered by unsafe behaviour. In fact, the HSE reports that up to 80% of accidents are attributable to “human error”. For example, climbing over assembly line barriers, not reporting machinery defects and not replacing worn-out personal protective equipment (PPE) are all unsafe acts. They are in the direct control of the people engaging in them and may therefore be targeted for improvement via behavioural safety.
Central to all behavioural safety initiatives is the view that injuries and illnesses are the result of ‘unsafe acts’ by workers, and to prevent this, safety managers should target specific behaviours and attempt to change them. Behavioural safety is also frequently linked to punishing ‘bad’ health and safety behaviour and rewarding good practice.
What does behavioural safety involve?
A behavioural safety process typically involves closely observing and monitoring individual workers – both for safe and unsafe behaviour. At the end of the observation period, a report is compiled with the noted safe and at-risk behaviours, including their date, time and location.
Individual workers are then given feedback, and employers should engage workers in a discussion to better understand unsafe behaviour and recommend a better approach. Unsafe behaviour may see workers being disciplined until they ‘learn their lesson’ and agree to change the behaviour. If an employee’s behaviour doesn’t change, this may result in dismissal for gross misconduct.
Workers’ comments and reasons for their at-risk behaviour should be recorded, along with the suggested safe behaviour. Analysing report findings will help flag-up trends of at-risk behaviours, including where they’re taking place. To further identify repeat unsafe behaviours, behavioural safety processes often examine incident rates over the previous two to three years.
What are the problems with behavioural safety?
At its core, behavioural safety assumes that incidents are usually due to worker error. This assumption is strongly disputed, with many practitioners being of the opinion that accidents are primarily rooted in health and safety management failings. This theory is supported by the HSE’s claim that 70% of workplace fatalities and injuries are caused by management failings, which appears to contradict their above statement that up to 80% of accidents are attributable to human error.
Those disputing the behavioural safety assumption that workers are the primary cause of incidents concede that there will normally be multiple factors involved, and that injuries cannot simply be classified as having a single cause. These opposing views can partly be explained by the different ways of looking at incidents.
For example, if a worker slips on an unclean floor:
- The employer may take a behavioural safety approach, concluding that the incident occurred because the worker wasn’t looking where they were going, despite having been warned about the slip danger.
- A safety professional may claim it was because the worker wasn’t wearing the right shoes to protect against slipping.
- Meanwhile, a safety representative could argue that the slip happened because the floor was unclean. After all, before an unsafe behaviour can cause injury, there must be a hazard.
A further issue is that as behavioural safety is based on observation, it is not ‘idiot proof’. The observation period may miss what actually happens in the workplace, as people will inevitably act differently when they know they’re being watched. When by themselves, workers may remove PPE or not follow the instructions they’ve been given. Further, such acts are deliberate violations, not errors. Try convincing a worker who quickly clears a blocked production line that they’re violating safety and you’re likely to be greeted by a confused look.
Additionally, as behavioural safety focuses on the end point of a chain of events that lead to a worker doing something wrong, it doesn’t address the question of who decided the work speed, productivity level, shift pattern, etc., and how such factors relate to safety.
What does the law say?
Health and safety law is very clear. The Management of Health and Safety at Work Regulations 1999 together with the Health and Safety at Work etc Act 1974 provide that hazards must be identified through a suitable and sufficient risk assessment and any risk removed or reduced “as far as is reasonably practicable”.
Employers are expected to reduce risk in line with what’s called a “hierarchy of controls”. This ranks which part of the risk reduction process should be attempted first. These prevention principles come from a European “Framework Directive” (89/391/EEC), which provides that employers must begin by avoiding risks. Where risks cannot be avoided, they should be evaluated and combated at source – reducing them by introducing safe(r) systems of work.
The hierarchy of controls is as follows (from most to least effective):
1. Eliminate the hazard (e.g. remove a dangerous machine, avoid work at height, etc.)
2. Substitute the hazard with a safer alternative (e.g. replace equipment with a safer version)
3. Use engineering controls to separate the worker from the hazard (e.g. local exhaust ventilation, machine guards, etc.)
4. Use administrative controls to reduce risk (e.g. provide training, develop safe systems of work)
5. Provide PPE to protect the worker (e.g. gloves, protective hearing devices, hard hats, respirators, etc.)
Behaviour safety focuses on fixing the unsafe acts of workers and modifying their behaviour. However, by concentrating on workers’ actions and, for example, favouring PPE and training as the main ways to prevent injury, behavioural safety turns the hierarchy of controls on its head. As a result, many ‘pure’ behavioural systems will not be conforming with UK or European law.
Should you therefore ignore behavioural safety?
In a word, no. However, behavioural safety is NOT a substitute for removing or controlling risk – that must be your priority. Once ways of removing or controlling hazards are in place, then reinforcing safer behavioural ways of working can be an important added weapon in reducing injury and illness.
How can employers promote behavioural safety?
A planned schedule of events should combine to create overall continuous improvement. This often begins with briefing sessions for all those involved. Observers should be trained to identify unsafe/safe behaviours and compile checklists. Observation should be carried out for a week or so to establish a baseline with which subsequent performance can be compared. On establishing the average baseline score, goal-setting meetings should set improvement targets. Monitoring behaviour should continue.
Observation scores should then be analysed so that detailed feedback can regularly be given to those concerned. The data should also be analysed for trends so that improvements can be highlighted and praised or corrective action taken.
On the basis of ‘what gets measured gets done’, observers should continue regularly monitoring safety behaviour. The greater the observation, the more reliable the data will be, and the more likely that safety will improve.
For example, if someone is observed coming down stairs without holding the handrail, they may change their behaviour to that of holding the handrail.
Workers should be fully engaged in safety management. Traditionally, safety management is top-down driven and often becomes stuck at front-line management level. However, workers most likely to engage in unsafe acts or be hurt are therefore traditionally divorced from the safety improvement process.
Employers can overcome this by purposefully involving those most likely to be hurt so that they are actively engaged in eliminating unsafe behaviours.
NB: Without widespread workforce involvement, ownership of and commitment to the process will be lacking and the initiative will likely fail.
Focus on the small proportion of unsafe behaviours that are responsible for the lion’s share of your safety incidents. Systematically examine your incident records to identify these behaviours. Categorised checklists (such as housekeeping, use of tools, PPE, etc.) should then be presented to employees for their approval or ‘buy-in.’
As the beahvioural safety process matures and original unsafe behaviours are eliminated or brought under control, other unsafe behaviours should be identified and placed on checklists.
Feedback is key to improvement. It helps overcome apathy and allows focused improvement to take place. Behavioural safety feedback usually involves:
- Verbal feedback– given to workers at the time of observation.
- Graphical feedback– where trends of weekly behavioural performance on large graphs are strategically placed in workplace locations.
- Weekly tabulated feedback reports– discussed by management and/or work teams on a monthly basis.
Observation scores should be turned into metric form, usually the percentage of behaviours performed safely. Examining data trends may also reveal where barriers to improvement lie.
Providing finely detailed feedback to those concerned may allow corrective action for persistent unsafe behaviour or provide positive reinforcement to those working safely. In this way, particular work processes that unintentionally lead workers to behave unsafely may be identified.
Failure of a behavioural safety initiative is almost always due to a lack of managerial commitment and support to the process. Therefore, managers’ and front-line supervisors’ demonstrable commitment to the process is vital.
Commitment can be demonstrated by:
- Allowing observers time to conduct observations.
- Giving praise and recognition to those working safely.
- Providing the necessary resources and assistance for corrective action to take place.
- Helping set up and run regular feedback sessions.
- Generally promoting the initiative whenever and wherever possible.
Hands-on Health & Safety support
Need a helping hand creating a safe working environment, implementing robust risk management procedures and developing a positive health and safety culture? From expert training and risk assessment support to Behavioural Safety Programmes and Safety Culture Surveys, our team of experienced safety specialists can help you to assess your current performance, promote safe and compliant behaviours and raise standards across your organisation.
Find out more about our Health & Safety support for employers or call 0345 226 8393 now to discuss your specific needs.