Blog
Electrical safety | A brief guide for employers
Written by Hannah Kennedy on 12 February 2021
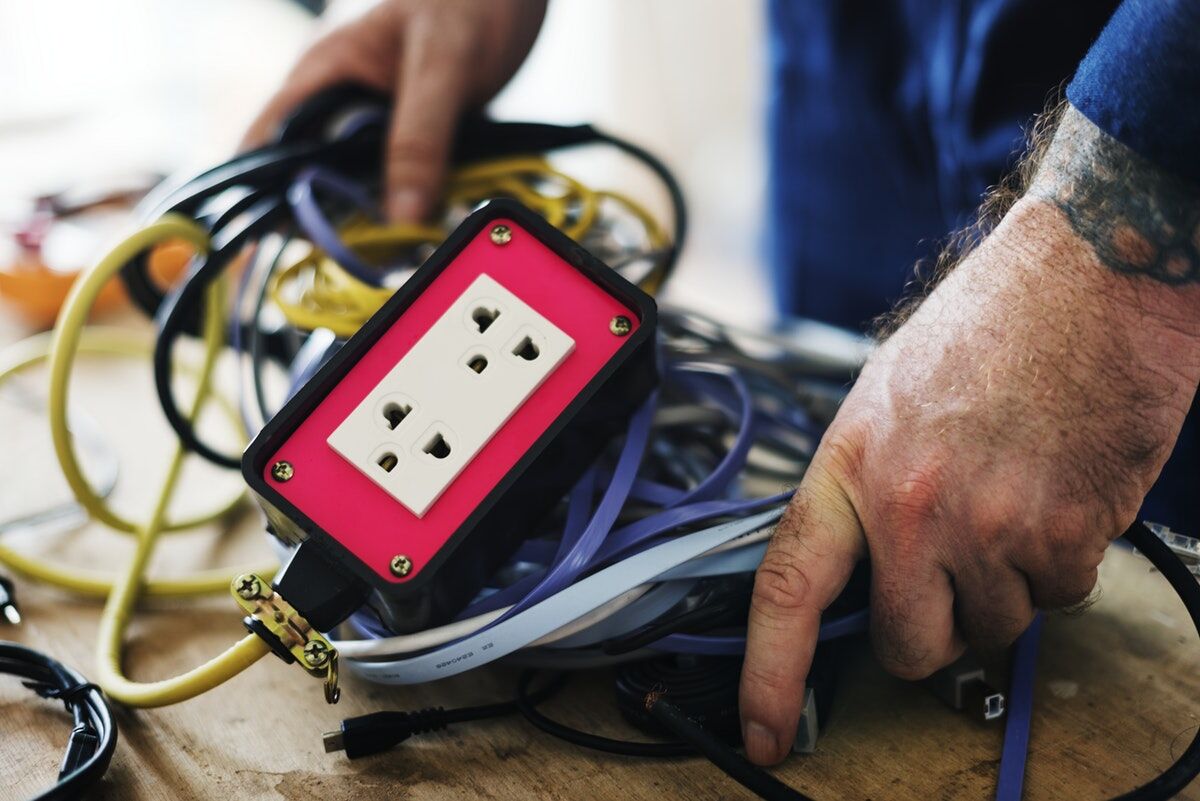
With the ability to cause damage to property, serious injuries and even fatalities, electrical safety should be a concern for all organisations.
Common electrical hazards
Voltages over 50 volts AC or 120 volts DC are considered hazardous. Workers can be seriously harmed when exposed to “live parts” or through conducting objects or materials. People most at risk of electrical injury include:
- Maintenance staff.
- Those working with electrical plant equipment and machinery.
Employees should only work with electrical equipment if having suitable training, knowledge, experience and supervision.
Shocks from equipment can cause severe injury. Lower voltages can reduce or remove the risk of shocks and burn injuries, and battery-powered tools are safest. Where possible, consider using lower voltage portable tools at 110 volts.
Do you need support?
Speak to us for an honest, no obligation chat on:
0345 226 8393 Lines are open 9am – 5pm
Causes of injury
Injuries are commonly the result of:
- Faulty of bare wiring
- Incorrectly replaced fuses
- Poor training
- Mixing water and electricity
- Misuse of equipment or using equipment that’s known to be faulty
- Overloaded or damaged plugs, sockets or cables (faulty or overloaded equipment can lead to fires)
Electricity can also ignite flammable or explosive atmospheres, for example around refuelling areas or in spray paint booths.
HR Manager, Empire Cinema
Electrical safety legislation
The Electricity at Work Regulations 1989 apply to all aspects of electricity use within the workplace. They place duties on employers to prevent danger, including:
- Ensuring electrical systems are safely installed and protected to prevent danger.
- Maintaining electrical systems as necessary to prevent them becoming dangerous.
- Carrying out work on electrical systems in ways that prevent danger.
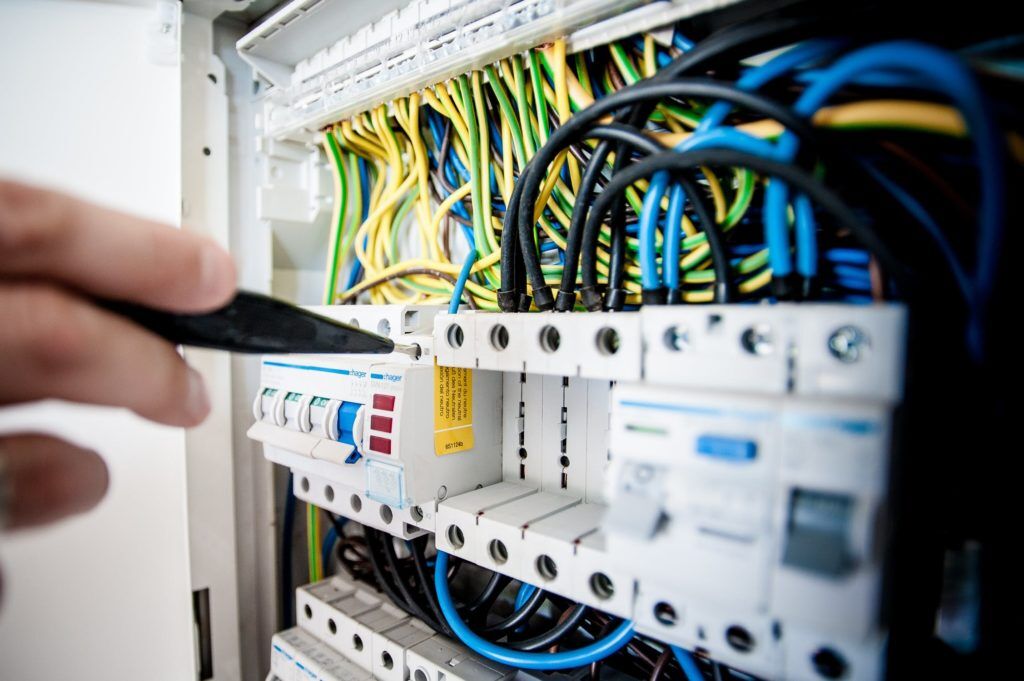
Electrical safety precautions
Taking simple precautions can significantly reduce the risk of electrical safety incidents.
Electrical equipment should, on a regular basis, be visually checked “before use” to spot early signs of damage or deterioration. Visual checks are often backed up by portable appliance testing (PAT). While not a legal requirement, PAT testing as part of your safety system can demonstrate your electrical equipment is in good working order and safe to use. Remember to include cables and transformers in any checks.
Other precautions include avoiding overloading sockets by providing enough plug-outlets.
You should take into account the following about electrical equipment:
- Where it’s used (i.e. is it used in a harsh environment, such as in extreme temperatures or corrosive conditions?). You should use a residual current device (RCD) or lower voltage tools in harsh environments. RCDs detect some but not all faults in the electrical system – they then quickly break the electrical supply.
- How often it’s used (equipment that’s used harshly should be tested more frequently than equipment that’s less likely to become damaged or unsafe).
- Type of equipment (i.e. if it’s portable or transportable).
You should also:
- Switch off appliances at the mains at the end of the working day.
- Switch off and unplug equipment before cleaning it or making adjustments.
- Provide an accessible and clearly identified switch near fixed machinery to cut off power in an emergency.
Equipment should additionally be formally tested by a competent person. Testing should be frequent enough that there’s little chance your equipment will become dangerous in the meantime.
Risk assessment
The best way to guage the electrical risks in your organisation and how to address them is by carrying out a risk assessment. Discuss any issues highlighted with staff.
Legislation requires employers to decide on the frequency of testing and inspection of electrical equipment based on the findings of a risk assessment. It’s good practice to write down how often each piece of equipment is to be checked – make sure the checks are carried out and keep a record of the results.
How often checks are carried out will need to be altered according to the number and severity of faults identified. If you find or suspect a fault, stop using the equipment immediately and remove it from use.
Further guidance
For more practical advice, see the HSE’s guidance Electrical safety and you: A brief guide.
Need a helping hand?
Health and safety can be a large undertaking if you don’t have the time of expertise. That’s why thousands of organisations choose to alleviate this burden through outsourcing their health and safety management to Ellis Whittam. Delivered through dedicated Health & Safety Consultants, our unlimited, fixed-fee service gives you access to sensible, proportionate advice on all aspects of compliance, plus award-winning software, document templates and training materials to keep your organisation on the right track.